- Sensors and Measuring Devices:
Quality automation often begins with the use of various sensors and measuring devices capable of monitoring the physical or mechanical properties of the product. Implementation may include sensors for measuring dimensions, temperature, color, weight, pressure, and other parameters.
- Visual Inspection:
Cameras and 3D scanners are used for visual inspection of products. This technology allows the detection of defects, deficiencies, and deviations from standard specifications. Advanced machine learning and image processing algorithms can automatically identify and classify problems.
- Automated Inspection Stations:
In an industrial environment, automated inspection stations can be created to perform various tests and examinations of products. This may include testing electrical properties, functionality, material strength tests, and more.
- Data and Analysis:
Data obtained from sensors and measuring devices are collected and analyzed to determine product quality. Advanced software can perform statistical data analysis and identify deviations from standards, helping predict maintenance needs or improvements in the production process.
- Feedback and Control:
Based on quality control results, feedback can be initiated into the production process. Automation allows quick responses to deviations and performs automatic regulation to achieve consistent quality.
Quality control automation has many advantages:
- Operational speed of feedback into production processes,
- Real consistency in product quality,
- Efficiency in controlling all product parameters,
- Real-time quality monitoring and analysis.
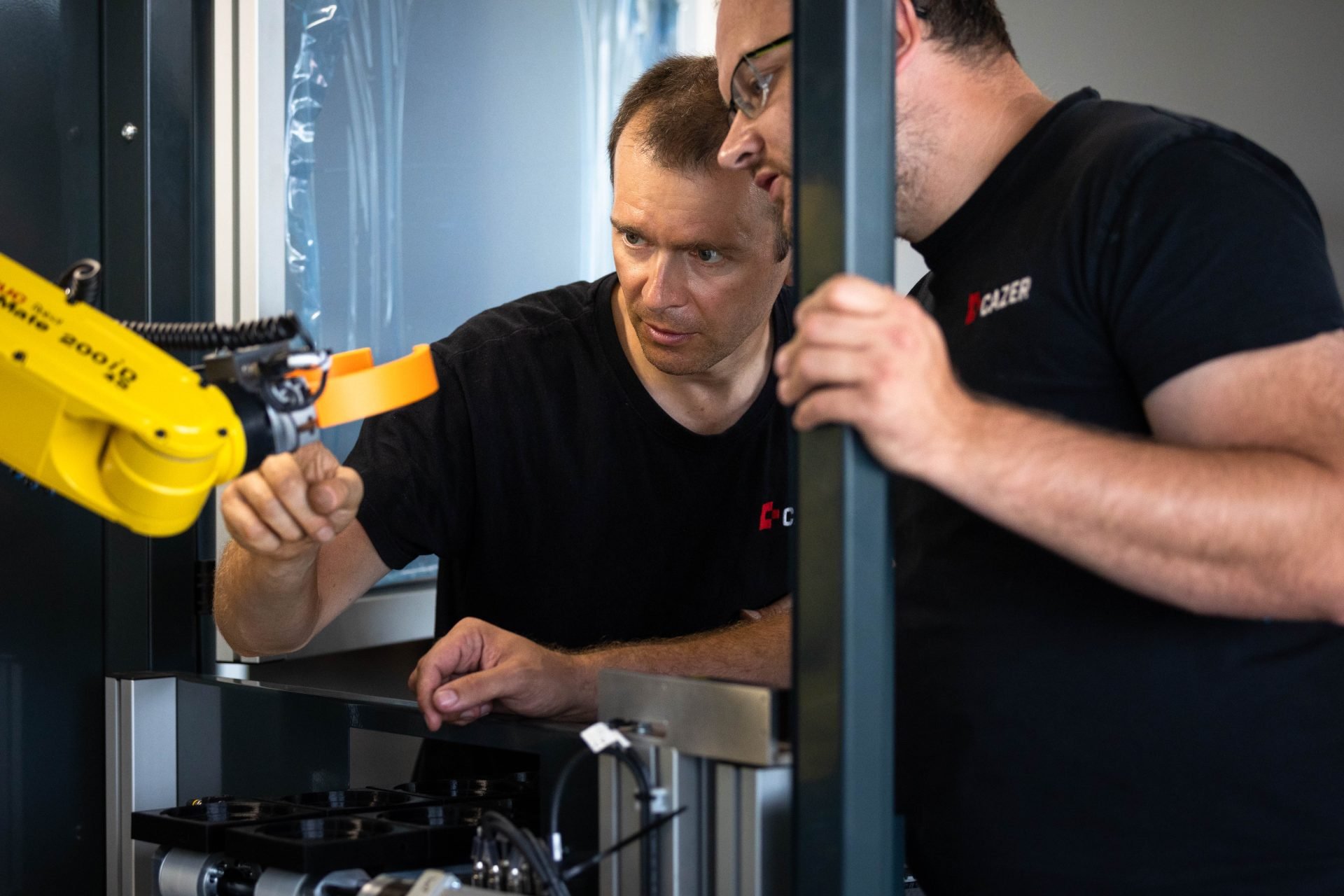
Our other products

Input analysis
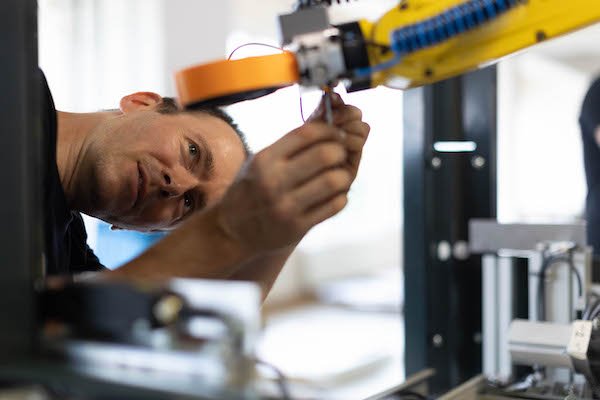
Robotization
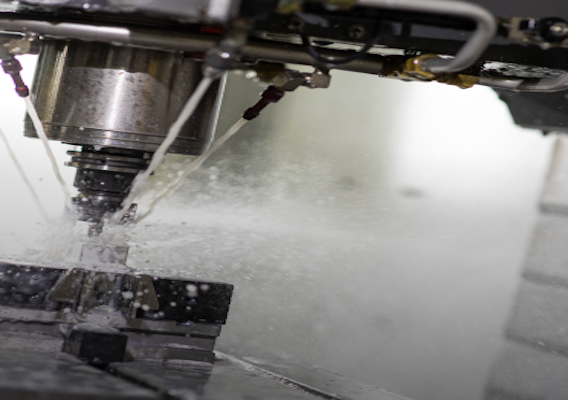
Single-purpose machines
to Z. The whole journey starts with your request or our visit.
